Insights into Excellence
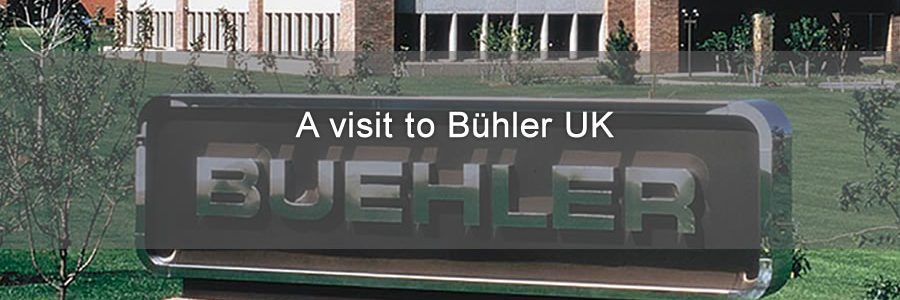
It is no secret that I believe Bühler in East London is one of the best places in the UK to see first-hand the application of a wide range of lean tools and techniques. On each visit, I have made over the last fifteen years, I have seen a new initiative or improvement that adds value to their customer – this time it was the introduction of a total synchro room for New Product Development in the middle of the main production floor. Last time it was the stores lock down. More on these later.
Unless you are in the food or automotive industries you may not have heard of The Bühler Group, but they are market leaders in industrial-scale process technologies and solutions. Very well-known are their automated rice milling solutions which process up to 30% of the world’s rice. Their technology also mills over 65% of the world’s wheat and 50% of the world’s cars feature die-casts made on Bühler machines. At the site in East London they design, assemble and export highly complex optical sorting machines for a wide range of industries. It is a low volume, highly complex assembly build. It is a centre of excellence within the Bühler Group which turns over CHF 2.5 billion per annum and has just over 10,000 employees worldwide.
Bühler’s continuous improvement and lean journey goes back around 20 years and was spearheaded by the previous MD Bruno Kilshaw, one of the first people I had the pleasure of working with on the visit programme, when it was known as Inside UK Enterprise. In 2004 they relocated from the original manufacturing site in Pudding Mill Lane due to compulsory relocation for the Olympics. The relocation provided them with the ability to create a flow line for assembly which had hitherto been impossible due to building constraints. They also made a decision at this time to focus on assembly and began to outsource fabrication and non-core manufacturing activities.
Main Production Line at Buhler Group, London
On the recent visit the Manufacturing Team provided our visitors with some great insights into the tools and techniques they have applied over recent years, I’ve summarised some of the ideas below:
Team Leader Programme
Bühler are one year into a two year team leader programme. About 18 months ago they recognised that their lean and CI activities were plateauing and to take the next step they needed to review and challenge their operational structure. Their approach was to create smaller, flexible teams that self-manage. The restructuring created a new wave of team leaders – with smaller focussed and more engaged teams. To ensure the newly created team leaders had the right skills to take on their new roles they invested in a programme of leadership training delivered by consultants RPO. This provided the newly created team leaders the skills to empower and engage their teams. Results so far have been impressive. Just one year in they have improved engagement from 6.7 to 8.5 out of 10. There has also been an 8% increase in productivity on site.
Bunker Sessions
Essentially the next evolution for 360 degree feedback, bunker sessions are an open and frank discussion where the team leaders bring feedback to the operations team and it is discussed in a closed door, no repercussion environment. This open and honest feedback loop has gone a long way to ensure both team leaders and operators feel they have a voice, are engaged and valued.
Total Synchro
Total Synchro is the Bühler name for their Lean and CI programme, there version of the Toyota Production System. The Total Synchro programme at Bühler focuses on creating a highly visual environment, where every employee can tell at a glance how the plant is performing.
One of the key elements that sets Bühler apart from many other manufacturers is the Total Synchro room, which employs the washing line tool to display the value stream from order through to delivery for every customer transaction. I always call this the marmite part of the tour. I’ve watched it evolve from a very basic single washing line or rope process which allowed you to visualise where in the factory orders were to being a more complex but still very simple system which allows instant visualisation of work orders. Initial reactions to the Synchro room are either ‘put it on a spreadsheet’ or ‘wow who moves all the paper’, but there is no denying that this system is effective in supporting the smooth running of the factory. It provides a focus for the cross-departmental daily Gemba, and means problems can’t be hidden or ignored.
Takt management & Visualisation
Takt time is the maximum amount of time in which a product needs to be produced in order to satisfy customer demand – it is essentially the pulse of production set to balance a line. Bühler introduced the use of takt and a pulse line when they set up the new production process in 2004. The takt allows them to flex up and down dependent on the demand of the customer.
On the introduction of the new team leader programme, the Operations Team created a magnetic tool to show how the takt could be impacted by kitting, line side supply and part shortages. At the change of each takt all the team leaders meet to review status allowing them to pre-empt or forecast any potential variance. Whilst this was intended as a temporary training tool it has now been adopted into day to day operations.
Fourth Industrial Revolution (4IR)
Bühler topped off a great day with an insight into how they as a company are staying ahead of curve in relation to 4IR. To maintain their leadership position Bühler recognised that they needed to understand and plan for the next generation of technology. They shared with us some concepts which they believe will transform the way they work in the future, ideas such as google glass which could aid picking and assembly, advanced engineering and robotic equipment which will reduce repetitive tasks and improve accuracy and consistency in production. All of these concepts will impact the look and feel of the factory of the future, they will impact supply, skills, training, build and distribution. Very similar to our recent visit to Kelloggs (Click here for the case study), Bühler showed that in a world of constant change and constant innovation it is necessary to plan for the unknown and increase flexibility.
Stores Lock Out and Value Stream Mapping
Value Stream Mapping has recently come back in to favour at the site, it was used in the early days of the new factory to assist with layout and line side kitting. The team recognised recently that it was worthy of resurrecting this useful tool to aid them evaluate and review processes on a localised level. On the visit they shared with us a project undertaken in stores where a value stream mapping exercise helped them to relay the stores area to speed up picking and improve accuracy. As part of the VSM activity they also instituted a stores lock down, so that engineers and operators couldn’t just wander in and help themselves to parts. This exercise has made significantly improved stock accuracy and improved picking rates.
Our thanks go out to Nigel Whittingham, Ivan Foxcroft, Peter Parmenter and all the team leaders who gave up their time to share best practice with others.